Machinery & Machinery Part Inspection - Machinery Quality Control
Machinery INSPECTION EXPERTISE
Machinery & Machinery Part Inspection – Machinery Quality Control
Machinery parts are the backbone across sectors like automotive, food processing, construction, and pharmaceuticals. Flawless functionality is vital for quality and safety, as even a single defect can have significant repercussions.
Â
At Tetra Inspection, we’re industrial guardians. Our meticulous inspection dissects each part destined for machinery, certifying quality, efficiency, and safety. We prioritize human safety, enhance product excellence, and protect business investments.
Â
Ensure your machinery’s optimum performance – Schedule a machinery parts inspection with us today.
MACHINERY PARTS INSPECTION
Importance Of Machinery Parts Inspection
When it comes to manufacturing, the meticulous inspection of machinery parts stands as a cornerstone for reliability and performance. From weld integrity and coating robustness to dimensional precision, the quality of these components profoundly impacts operational success.
Â
Let’s delve into why machinery parts inspection plays a pivotal role in ensuring impeccable manufacturing standards and seamless operational efficiency.
Welding Quality:
Effective welding ensures the structural integrity of machinery components. Inadequate welding can lead to fractures, weakening the entire structure. Regular inspection using non-destructive techniques like X-ray and ultrasonic testing is essential. Adhering to recognized standards such as ISO 3834 and AWS D1.1 assures weld quality, fostering reliability and safety.
Dimensional Accuracy:
Precise measurements are the bedrock of effective machinery performance. Deviations in dimensions can impede functionality and compromise the final product’s quality. Adhering to international standards such as ISO 1101 ensures uniformity in dimensions and geometric tolerances, enhancing compatibility and interchangeability.
Â
Coating Quality:
Machinery parts often face harsh environmental conditions, underscoring the need for robust coatings—quality coating shields against corrosion, wear, and erosion. Thorough inspection involving visual assessment, thickness measurement, and adhesion tests verifies coating durability. Compliance with standards like ISO 12944 is pivotal to achieving enduring protection.
machinery TESTING
Critical Elements Of Machined Parts Inspection
Machined parts inspection is a systematic approach to ensure that manufactured components meet specified requirements. Given the precision often demanded in the machining industry, several critical elements must be considered during the inspection process.
Â
Material Inspection
Before inspecting the machined part, confirming that the correct material has been used is crucial.
- Metal Analysis: Techniques such as spectroscopy can determine the composition of metals, ensuring that the correct alloy or grade has been used.
- Hardness Testing: It evaluates the material’s resistance to deformation. Standard methods include the Rockwell, Brinell, and Vickers tests.
Surface Finish Evaluation
The finish on a machined part can influence its functionality. As such, it’s an essential element of inspection.
- Surface Roughness Testers: These devices move a probe across the part’s surface to measure its roughness, determining if it’s within acceptable levels.
- Visual Inspection: A simple visual check under appropriate lighting can determine if the finish is acceptable for parts where aesthetics matter.
Functional Tests
For some components, it’s not just about their physical attributes but also about how they function.
- Assembly Testing: Some parts are designed to fit with others. Assembly tests ensure they integrate as intended.
- Motion Testing: For parts that are meant to move, such as gears or levers, a motion test can ensure they operate smoothly and without obstruction.
Dimensional Accuracy
This involves measuring the machined part to ensure it matches the specified dimensions.
- Coordinate Measuring Machines (CMM): These devices measure the physical geometrical characteristics of a part. By placing the amount on the CMM’s table, the machine can determine if the domain is machined to the correct specifications.
- Gauges and Micrometers: These hand tools are used to quickly check specific dimensions, such as the diameter of holes or the thickness of a feature.
Geometric Tolerances
Beyond simple dimensions, the geometric attributes of a machined part can impact its performance.
Â
- Form: This relates to the shape of a feature, such as straightness, flatness, roundness, or cylindricity.
- Orientation: This concerns the relationship between elements, like perpendicularity or parallelism.
- Location: This involves positional tolerances and ensures that features are in the right place.
- Runout: It measures the variance in a rotating part, guaranteeing smooth operation.
VITAL STEP IN THE machinery Inspection Process
Machinery Parts Inspection Process
The machinery parts inspection process is an organized sequence of actions and checks designed to thoroughly evaluate machine components’ condition, functionality, and integrity. This process helps ensure that every part aligns with industry standards, quality benchmarks, and safety regulations. So, how does this intricate dance of assessment unfold? Let’s explore it step by step.
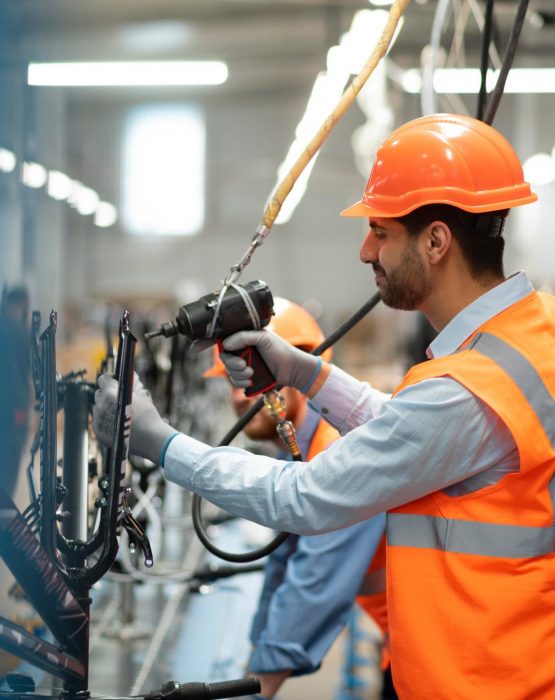
Verification of Design Accuracy:Â First Article Inspection
First Article Inspection or FAI ensures that the manufactured component aligns with the design specifications and drawings. Any deviation from the expected dimensions, materials, or functions is identified early, preventing potential issues in mass production.
Raw Material Analysis
The end product quality often hinges on the quality of the raw materials used. This is why it is important to assess the material properties like strength, durability, and resistance to environmental factors and verify that they meet the required standards.
Supplier Verification
Suppliers play a critical role in the machinery production line. Verifying their credentials and assessing their history of delivering quality parts is crucial.
Material Sampling and Verification:
Inspectors collect samples of the materials that will be used in the furniture, such as wood, fabric, and metal, to verify their quality and suitability for the intended purpose.
Reviewing Design Specifications:
Inspectors thoroughly review the design specifications provided by the manufacturer to ensure that they align with the desired quality and safety requirements.
Ensuring Factory Capabilities:
The inspectors assess the factory’s production capabilities, equipment, and workforce to determine if they have the capacity to meet the production demands while maintaining quality.
Visual Inspection
Inspectors check for defects like cracks, misalignment, or surface irregularities that might affect the part’s functionality or lifespan.
Dimensional Checks
Precision tools, like micrometers and calipers, measure parts and ensure they align with the specified dimensions.
Functional Testing
Parts are tested under operational conditions to see if they perform their intended function accurately and efficiently.
Â
Tolerance Testing
Machinery parts often need to function under varying conditions. This testing ensures that parts work within their operating conditions’ designated upper and lower limits.
The final inspection takes place at the end of the production cycle.
Assembly Inspection
Once parts are assembled, inspecting the machine as a whole is essential. This ensures that all parts fit well together and that the device functions as intended.
Â
Endurance and Stress Testing
Parts are subjected to conditions that mimic prolonged or extreme use to ensure they won‘t fail under strain.
Â
Quality Control Machine Testing
Specialized quality control equipment is employed to automate the inspection of parts, ensuring consistency and accuracy.
Â
Documentation Review
All inspection data, test results, and compliance verifications are documented. This provides a record for future reference and ensures that all inspections have been carried out as per the set protocols.
Applicable Standards For Furniture Quality Applicable Standards For Equipment Quality Control
Quality control isn’t merely about checking if a machine works. It’s about ensuring that machinery and its components adhere to established standards that dictate their performance, safety, and durability. These standards are not arbitrarily set; they result from extensive research, testing, and industry consensus. Let’s dive deep into the various standards applicable to equipment quality control.
- ISO 9001: Quality Management Systems ISO 9001 is arguably the most widely recognized and adopted standard globally. The focus on customer satisfaction, process improvement, and top management’s involvement ensures that companies consistently adhere to quality benchmarks and meet customer requirements. Many organizations consider ISO 9001 certification a testament to their commitment to quality.
- ASME Standards The American Society of Mechanical Engineers (ASME) standards are crucial, especially for mechanical devices and equipment. Given the widespread manufacturing and use of automated machines, especially in North America, ASME standards are vital in ensuring safety and performance. For industries that use boilers and pressure vessels, adherence to ASME standards is non-negotiable.
- IEC Standards In an increasingly digitized world where machinery integrates more electrical and electronic components, IEC standards gain prominence. They ensure that such machinery is functional, safe, and compatible with other electronic systems. For companies producing or using machinery with electronic components, IEC standards are pivotal.
- Industry-Specific StandardsWhile general standards like ISO 9001 provide a broad framework, industry-specific standards delve into particular sectors’ unique challenges and requirements. Adherence to these standards ensures that machinery meets the specialized needs of aerospace, automotive, and other industries. These standards often define the very baseline of quality and safety for their respective sectors.
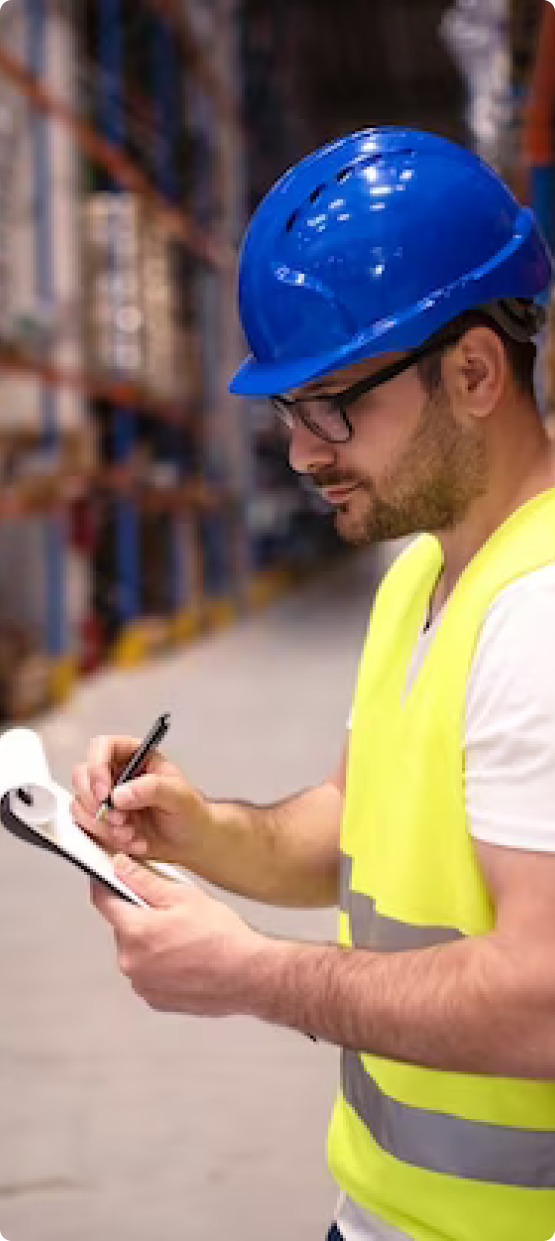
How Tetra Inspection Can Help With Machined Part Inspection Services
Advanced Quality Control Equipment
Tetra Inspection employs the latest quality control equipment, ensuring accurate and comprehensive assessment of machinery parts. From microscopic flaws to more significant structural issues, we leave no room for defects.
Experienced Team
We are proud to have a team of seasoned professionals with at least five years of experience who bring their expertise to the table. Their deep-rooted understanding of machinery and continuous training ensures they are always at the forefront of inspection best practices.
Customized Solutions
Recognizing that every manufacturer has unique needs, we offer customized inspection solutions. With specific requirements, production scales, and challenges of each client, we design our inspection services accordingly.
Transparent Reporting
Our transparent reporting system ensures that manufacturers are kept in the loop at every stage of the inspection process. Detailed reports, backed by digital evidence insights and recommendations, allow manufacturers to make informed decisions.
Schedule Your Machinery Parts Inspection Today
Rely on our team of highly seasoned experts for meticulous machinery parts inspection, effectively minimizing risks and ensuring strict adherence to international standards.
Â
BLOG
Related Articles
shipment, minimizing risks and ensuring compliance with international standards.